Spacecraft monitoring system
The system, composed of a several micro-cameras and a control unit can be used for:
- Antenna deployment monitoring
- Solar panels deployment monitoring
- Health check
- Anomaly investigation
- Failure assessment
Heritage on BepiColombo and Sentinel-1a.
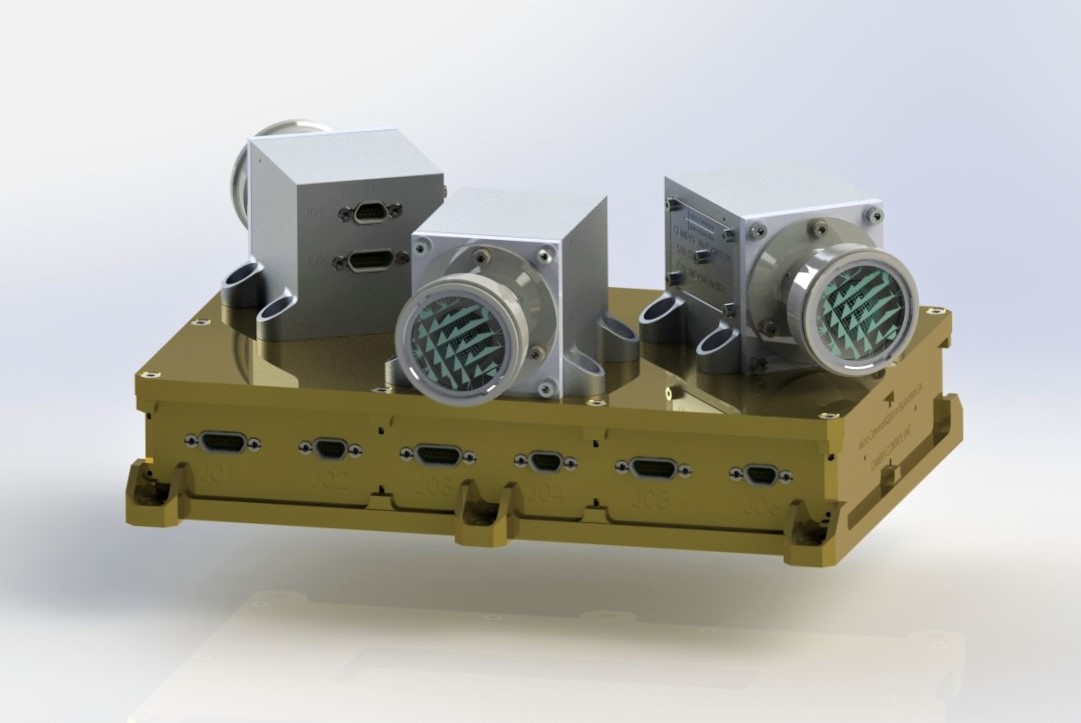

Multi-Purpose Imaging System
Compact multi-sensors system providing imaging capabilities with different fields of view and advanced processing capabilities. It is upgradable and allows connection and control of other sensors, motors, etc., as well as diverse TM/TC connections to spacecraft or antennas.
It is composed primarily of 2 to 4 cameras (MCAMs) and a Control & Image Processing Unit (CIPU).
Applications range for spacecraft health check, objects detection and identification, debris monitoring and mapping, in-orbit services visual support (docking, identification, monitoring), launcher separation video, scientific and planetary exploration applications, etc.
Photogrammetry System
The system, composed of a set of micro-cameras, integrated with the so-called “multi-station” concept, results in a small and light camera hardware, low thermal losses in the thermal-vacuum chamber and no complex feed-throughs required. The goal is to achieve better than 10 parts per million (ppm) as measurement accuracy for large objects inside any suitable test facility in Europe.
...
The conceptual diagram of the complete micro-camera system is based on a configuration derived from the so called “multi-station” concept. The system is based on four cameras, each equipped with a ring flasher and controlled by a single control unit (power, command and image acquisition), which insures also the synchronization with the four flashers. The flasher power supply cabling has to be separated from the micro-camera cabling for EMI reasons. A roll capability around the optical axis could be provided for each camera to increase the videogrammetry measurement precision by acquiring additional images for the same camera position.
The added value provided by the versatility of the micro-camera approach is very high considering the potential tailoring capability for a variety of testing applications, for instance where the dimension of the chamber or of the test object, the possibility of mechanical supports inside the chamber or its access from the outside dictate severe restrictions. There is much less hardware involved. It is easier to access the components for repair and/or maintenance. The required support equipment and harness for testing is very limited also for very specific applications due to the extremely low weight (~100g) and dimensions of the micro-cameras and of the other components. There is no need for special environmental protections. The cameras are already qualified for thermal-vacuum conditions, with very low operational temperature, down to -120°C.

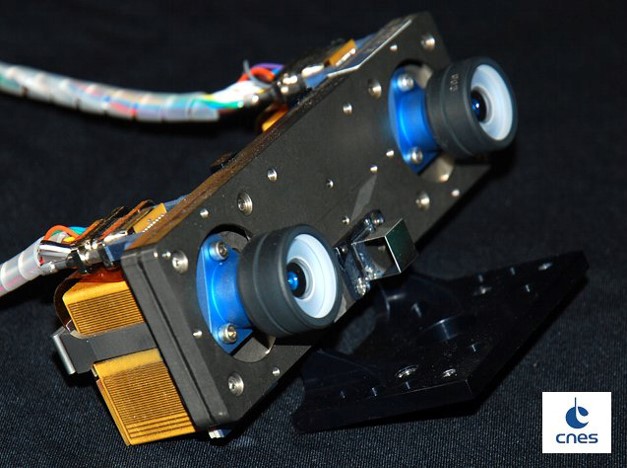
Stereo bench
Stereoscopic Imaging System for Planetary Rover developed for CNES
Stereoscopic bench with optical angular stability insured after launch, travel and landing mechanical and thermal stresses
Mass 400g
Optical axis stability < 3 microns
Vibrations (15 g rms) and thermal cycle down to -120°C
Electrical Ground Support Equipment
Support equipment to control and power the cameras with a PC or a laptop.
